The Radius Pultrusion™ process offers numerous benefits for those seeking advanced composite solutions. The curved pultruded profiles created using Radius Pultrusion unlock an array of new applications in a variety of markets, including automotive, infrastructure, agriculture, and aerospace.
- Closed section: A closed section offers customers a stronger profile, leading to increased torsional stiffness and performance. Reduced mass and cost can also be achieved through closed section design.
- Multi-Hollow profiles: Improves lightweighting, section stability and crush performance.
- High volume: Pultrusion provides all the benefits of a continuous process without the need for additional labor or floor space.
- Variable length: Varying lengths can be produced from the same tooling.
- Curved components: Adding curvature increases flexibility in the design of end products, and unlocks new applications for composites.
NON-CRIMPED FABRICS
Nearly any type of fiber can be used within Shape’s pultrusion processes, including unidirectional, biaxial, triaxial and even quadaxial reinforcements. Carbon fiber, E-glass, S-glass, A-glass, aramid, basalt and other natural fibers are among the tailored laments Shape has experience with.
Each product solution goes through extensive engineering, testing and review to ensure the right fabrics are selected to optimize performance, mass and cost. In addition, Shape works closely suppliers like Vectorply, Composites One and SGL Group to provide a robust and cutting edge catalog of fabrics.
RESIN SYSTEMS
A nearly endless variety of custom formulated thermoset resin systems, including polyurethane and epoxy formulations, are compatible with Shape’s pultrusion technology. To bring more flexibility to customers Shape partners with top industry suppliers like BASF, Scott Bader, Huntsman and Covestro on resin system development.
Shape’s global product design teams are capable of helping customers at all levels of the development process. The company’s robust technical services include:
- Global in-house CAD
- Global in-house CAE
- Physical Test Lab
Shape’s expertise and capabilities don’t end after cutoff. As part of their environmentally controlled manufacturing facility the Shape composites team can perform a number of secondary operations, including:
- CNC machining
- Post curing capabilities
- Automated assembly
- Automated adhesive application
- Advanced GD&T and gauging techniques
- CAMX ACE award finalist (2017)
Infinite Possibility For Market Growth - IACMI member
- Automotive OEM supplier
COMPOSITES NEWS
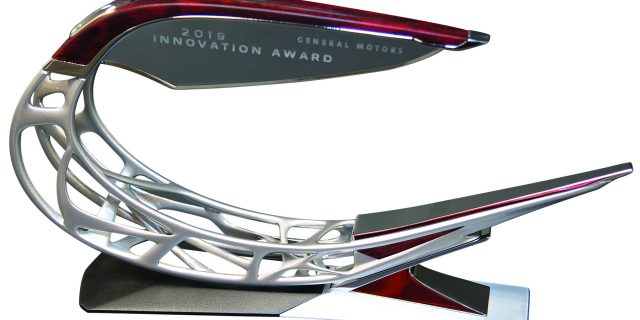
General Motors Honors Shape Corp. as Winner of Coveted Supplier Innovation Award
Grand Haven, MI – Shape Corp. was named a GM Innovation Award winner during a virtual ceremony to celebrate the recipients of General Motors’ 28th annual Supplier of the Year awards on Wednesday, June 24. GM’s Innovation Award recognizes the top suppliers among thousands of global contenders that introduced innovations that deliver cutting-edge technologies that substantially […]
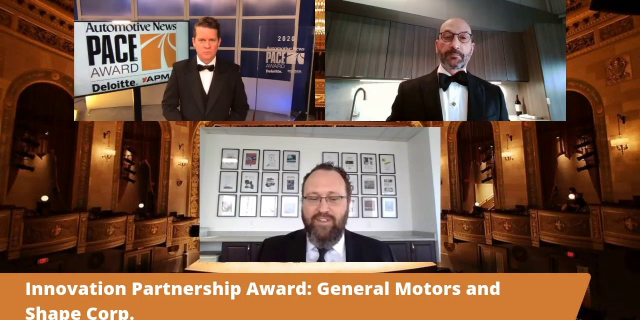
SHAPE CORP. WINS INNOVATION PARTNERSHIP AWARD FOR COLLABORATION ON CARBON FIBER BUMPER BEAM
Shape Corp., a tier one automotive supplier was awarded a 2020 Automotive News PACE (Premier Automotive Supplier’s Contribution to Excellence) Innovation Partnership Award in conjunction with General Motors for their collaboration in engineering and manufacturing the automotive industry’s first curved, multi-hollow pultruded carbon fiber bumper beam for the 2020 Chevrolet Corvette Stingray. The Innovation Partnership […]
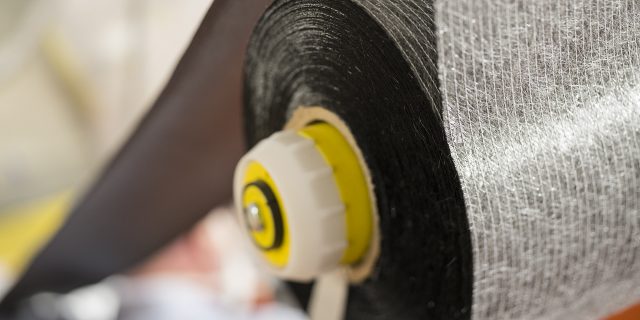
Pultrusion Picks Up Speed in Automotive Applications
Pultrusion is one of the most cost-effective processes for manufacturing high-volume composite parts. Recently Composites World featured Shape Corp’s recent composites advancements as an example of the growth composites are experiencing in the automotive market place. To read the full article click here.
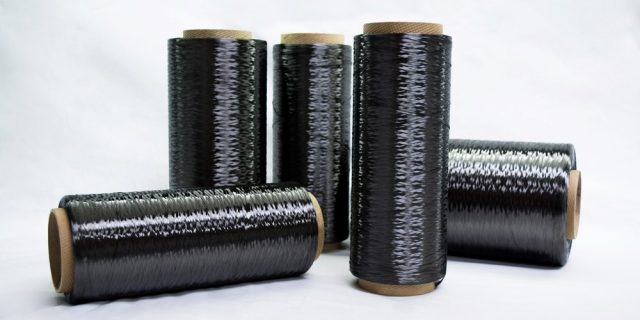
The Case for Carbon Fiber
Applications for carbon fiber in a vehicle’s body structure continue to gain positive momentum, with BMW’s i3 being a prime example. Advancements are being made throughout the industry and the case for carbon fiber is becoming more viable. Learn more by reading a recent article from Automotive Manufacturing Solutions. Read more…
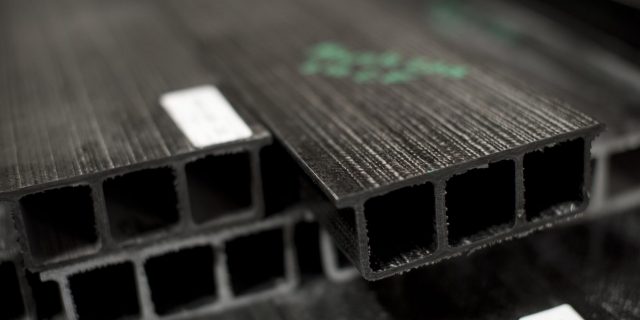
Mechanical Testing of Composites
Finding a consensus on the most important type of mechanical test for composites can be a difficult task, especially with the variety of applications composites are being used for. Composites World columnist Dr. Dan Adams, explores this topic in a recent article. Read more…
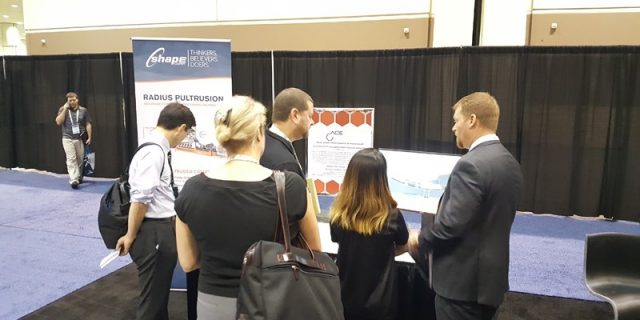
Shape Makes the ACE Finals at CAMX
Shape’s innovative spirit was on display at the 2017 CAMX—the premier composites and advanced materials event and for four days the center of the composites world. Shape was in attendance as a finalist for an Award for Composite Excellence (ACE), the composite industry’s stand out award showcase. The ACE awards are an annual competition hosted by […]
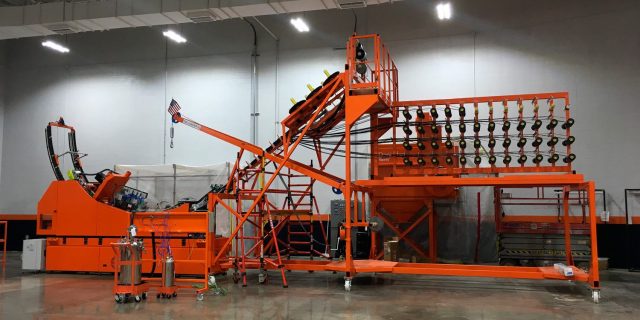
Pioneering in Pultrusion
Composites Manufacturing Magazine featured some very exciting pultrusion technology Shape is licensing from Thomas Technik + Innovation. You can read more about is creation, development and wide range of applications here.
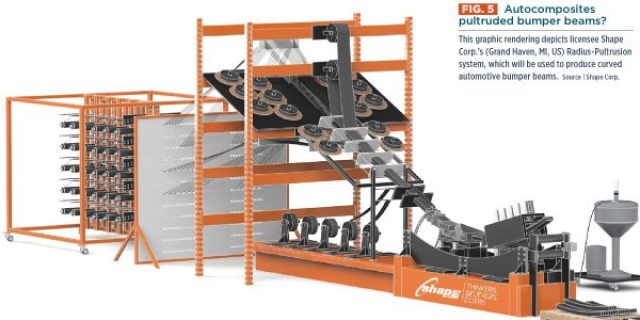
Shape featured in Composites World Magazine
Shape’s bright future and the innovative radius-pultrusion system are featured in the June edition of Composites World, the world’s leading composites publication. The center fold article profiles Thomas Technik’s curved pultrusion process and features details regarding Shape licensing the technology for use in the automotive industry. While a number of licensees were highlighted in the […]

Shape Takes Steps Toward Innovation
With the automotive industry heavily focusing on lightweighting for improving fuel economy, Shape as always, is eager to support our customers with innovative, lighter weight components. For years we’ve been developing bumper solutions that are some of the best in the industry, utilizing ultra-high strength steels, unique aluminum alloys, and patented cross section designs. Still […]